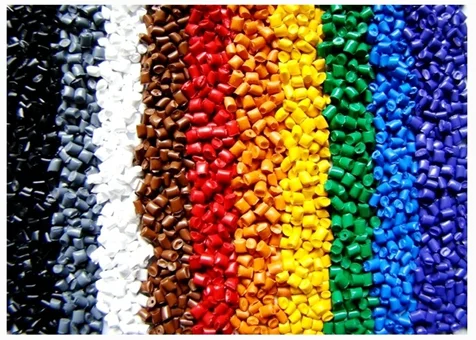
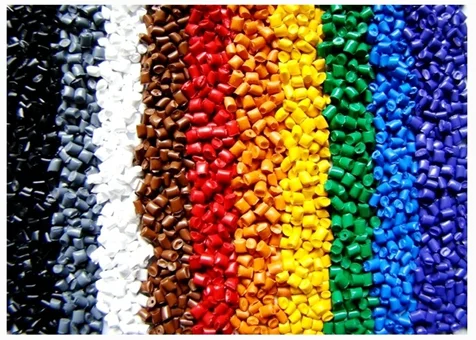
In the world of advanced materials and engineering, thermoplastics have become a remarkably versatile and innovative solution, driving transformative changes across multiple industries. One particularly thrilling frontier of progress involves the development of specialty profiles with these materials. In this article, we'll explore the dynamic realm of thermoplastic engineering specialty profiles and how they fuel innovation across diverse applications.
Understanding the Potential of Thermoplastics:Prior to delving into the specifics of specialty profiles, it's essential to grasp the exceptional attributes of thermoplastics. These polymers are defined by their unique property: they become pliable when exposed to heat and subsequently solidify as they cool. This distinctive feature endows them with remarkable versatility, making them suitable for a wide spectrum of applications across industries. The advantages of thermoplastics are indeed multifaceted, encompassing exceptional durability, lightweight characteristics, resistance to chemical degradation, and outstanding thermal and electrical properties. Their inherent strength allows them to withstand the rigors of diverse environments, making them a reliable choice for challenging applications. As we explore the remarkable world of thermoplastics, we'll uncover how these properties translate into ground-breaking solutions across various sectors. The adaptability and resilience of thermoplastics continually fuel innovation, making them a driving force in modern engineering and design.
Exploring Thermoplastic Engineering Specialty Profiles:Customized Design: The precision involved in creating thermoplastic specialty profiles represents a revolutionary leap forward in manufacturing. This precision empowers manufacturers with the unique capability to finely customize profiles, tailoring them with precise shapes, sizes, and geometries to fulfil the exact requirements of specific applications. Such a high degree of customization proves invaluable, especially in industries like aerospace, automotive, and construction, where every component must adhere to rigorous standards. Whether it's creating intricately shaped components for aircraft or precisely fitting parts for automobiles, thermoplastic specialty profiles offer a level of adaptability that significantly streamlines the manufacturing process and enhances overall product performance. This level of precision not only boosts the efficiency of production but also supports advancements in various sectors by meeting the exacting demands of modern engineering and design. The marriage of cutting-edge technology and customization found in thermoplastic profiles has opened new doors to innovation across industries.
Weight Reduction: In sectors where weight is of paramount importance, thermoplastic specialty profiles provide an elegant and efficient solution. These profiles surpass traditional materials like metals by virtue of their remarkable lightweight attributes. This not only aids in diminishing fuel consumption within the transportation sector but also elevates energy efficiency across a diverse range of applications.
Corrosion Resistance: One of the inherent merits of thermoplastics is their inherent resistance to corrosion, which eliminates the need for additional coatings or treatments to protect them from environmental elements. This intrinsic durability makes them the optimal choice for use in challenging environments, such as offshore drilling platforms and chemical processing plants. Their ability to withstand corrosive forces ensures longevity and reliability in these demanding settings. Thermoplastics serve as a dependable choice, saving time and resources that would otherwise be spent on maintenance and protection measures. Their resilience stands as a testament to their suitability for the most arduous industrial conditions, ensuring a cost-effective and efficient solution.
Ease of Assembly: Collaborating with thermoplastic specialty profiles is a straightforward and efficient process, streamlining assembly tasks. Manufacturers enjoy significant time and labour savings as these profiles can be readily cut, welded, or moulded into intricate forms, optimizing the manufacturing workflow. The versatility of these profiles simplifies the production process, allowing for rapid adaptation to specific project requirements. This ease of manipulation empowers manufacturers to achieve intricate designs without the complexities associated with other materials. The cost-effective and time-efficient attributes of working with thermoplastic specialty profiles make them a preferred choice for enhancing manufacturing processes. This adaptability and ease of use contribute to improved productivity and overall operational efficiency, fostering innovation and progress in numerous industries.
Applications of Thermoplastic Specialty Profiles:Aerospace: In the aerospace sector, the paramount concern is weight reduction. Thermoplastic specialty profiles have found their niche in various components, such as interior panels, air ducts, and brackets, playing a pivotal role in enhancing fuel efficiency. These profiles are integral in the pursuit of reduced weight, as they contribute to the overall goal of optimizing aircraft performance. Their application not only reduces fuel consumption but also enhances the aerodynamic performance of aerospace systems. The adoption of thermoplastic specialty profiles has become a cornerstone in the quest for more sustainable and eco-friendly aviation solutions. Their lightweight attributes offer an innovative approach to addressing the challenges of modern aerospace engineering. As we witness a shift towards cleaner and more efficient aircraft, thermoplastics continue to be at the forefront of driving transformative changes in the industry.
Automotive: The automotive industry enjoys substantial advantages from the integration of thermoplastic profiles into various components, including door panels, bumper beams, and interior elements. These profiles serve a dual purpose by reducing the overall weight of vehicles while concurrently enhancing safety standards. Their lightweight attributes contribute to improved fuel efficiency and reduced environmental impact, aligning with the industry's focus on sustainability. Furthermore, these profiles offer an innovative solution to safety concerns by providing impact resistance and crash protection. This duality of purpose makes thermoplastic profiles a valuable asset in the pursuit of more efficient, eco-conscious, and safer vehicles. As the automotive sector evolves, the utilization of these profiles stands as a testament to the industry's commitment to innovation, performance, and the well-being of drivers and passengers.
Construction: In the construction industry, thermoplastic profiles play a pivotal role, finding application in crucial structural components such as window frames, insulation, and drainage systems. These profiles are essential in upholding the integrity of construction projects, contributing to the overall durability and longevity of the built environment. Their robust resistance to diverse environmental factors, including moisture, temperature fluctuations, and corrosive agents, ensures that structures remain resilient and reliable over time. By incorporating thermoplastic profiles into construction, builders and engineers prioritize sustainability, as these materials are known for their long-lasting performance and reduced maintenance needs. The versatility of these profiles allows for creative design and easy installation, making them a favoured choice in modern construction practices. As the construction industry evolves to meet the demands of the future, thermoplastic profiles are at the forefront, serving as an emblem of innovation and progress in infrastructure development.
Medical Devices: Within the medical domain, the utilization of thermoplastic profiles is prevalent in the creation of essential components like tubing, connectors, and housing. These profiles are favoured due to their exceptional biocompatibility, ensuring they can safely interact with biological systems and tissues without adverse reactions. Furthermore, their sterilizability attributes make them an ideal choice for maintaining rigorous hygiene standards in medical applications. The adaptability of thermoplastic profiles allows for the precise customization of these critical components, meeting the unique requirements of the healthcare industry. This adaptability not only enhances patient safety but also streamlines the manufacturing process, reducing costs and improving overall efficiency. As the healthcare sector continues to advance, thermoplastic profiles remain a cornerstone of innovation, providing solutions that prioritize patient well-being, performance, and compliance with stringent medical standards.
The captivating world of thermoplastic engineering specialty profiles is reshaping innovation across a wide array of industries. Customization, weight reduction, corrosion resistance, and ease of assembly are just a few of the numerous benefits they offer. As these materials continue to evolve and discover new applications, the potential for ground-breaking innovations in engineering and manufacturing knows no bounds. Keep a close eye on the ever-evolving landscape of thermoplastics as they sculpt the future of technology and design.
#ThermoplasticEngineering #SpecialtyProfiles #InnovationInEngineering #Customization #WeightReduction #CorrosionResistance #VersatileMaterials #ManufacturingAdvancements #AerospaceTechnology #AutomotiveIndustry #ConstructionInnovations #MedicalDeviceMaterials #SustainableSolutions #BiocompatibleProfiles #EfficientManufacturing #EnvironmentalDurability #FutureOfTechnology #DesignInnovation #AdvancedMaterials #EngineeringSolutions #ModernManufacturing #InnovativeDesigns #ThermoplasticApplications #DurableProfiles #EcoFriendlyMaterials